Unraveling the Secret of Porosity in Welding: Tips for Lessening Defects and Maximizing Quality
In the detailed globe of welding, porosity continues to be a persistent challenge that can significantly impact the quality and integrity of welded joints. As we dig into the depths of porosity in welding, uncovering the secrets to its prevention and control will be paramount for professionals looking for to master the art of top quality weldments.
Understanding Porosity in Welding
Porosity in welding, a common issue encountered by welders, describes the visibility of gas pockets or gaps in the bonded material, which can jeopardize the integrity and quality of the weld. These gas pockets are typically trapped throughout the welding procedure because of various factors such as improper securing gas, polluted base materials, or incorrect welding criteria. The development of porosity can compromise the weld, making it vulnerable to cracking and deterioration, inevitably causing structural failings.
Comprehending the root creates of porosity is critical for welders to successfully stop its incident. By recognizing the value of preserving proper gas securing, making sure the cleanliness of base materials, and maximizing welding setups, welders can considerably reduce the chance of porosity formation. In addition, using methods like preheating the base product, employing correct welding techniques, and performing extensive inspections post-welding can additionally aid in decreasing porosity problems. On the whole, a detailed understanding of porosity in welding is important for welders to generate top quality and long lasting welds.
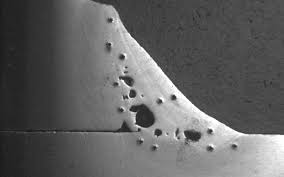
Typical Root Causes Of Porosity
When examining welding procedures for possible quality problems, recognizing the usual causes of porosity is essential for preserving weld honesty and stopping structural failings. Porosity, identified by the presence of cavities or gaps in the weld metal, can dramatically compromise the mechanical residential or commercial properties of a welded joint. One common reason of porosity is incorrect securing gas coverage. Inadequate protecting gas flow prices or incorrect gas combinations can cause climatic contamination, causing porosity development.
An additional widespread reason for porosity is the presence of moisture and impurities on the surface of the base metal or filler material. When welding materials are not properly cleansed or are subjected to high levels of moisture, the evaporation of these pollutants throughout welding can produce spaces within the weld bead. In addition, welding at incorrect specifications, such as excessively high traveling speeds or currents, can create too much turbulence in the weld pool, capturing gases and triggering porosity. By dealing with these usual causes through correct gas protecting, product prep work, and adherence to optimal welding criteria, welders can lessen porosity and enhance the top quality of their welds.
Techniques for Porosity Prevention
Applying effective preventive procedures is essential in decreasing the occurrence of porosity in welding procedures. One strategy for porosity prevention is making sure correct cleaning of the base steel prior to welding. Contaminants such as oil, grease, corrosion, and paint can bring about porosity, so detailed cleansing utilizing suitable solvents or mechanical techniques is important.

Utilizing top notch filler products and securing gases that are suitable for the base metal and welding process can significantly reduce the risk of porosity. Additionally, keeping correct welding criteria, such as voltage, existing, take a trip rate, and gas circulation price, is crucial for porosity prevention.
Additionally, employing proper welding techniques, such as keeping a regular traveling speed, electrode angle, and arc length, can aid protect against porosity (What is Porosity). Ample training of welders to guarantee they comply with best practices and top quality control procedures Check Out Your URL is additionally crucial in decreasing porosity flaws in welding
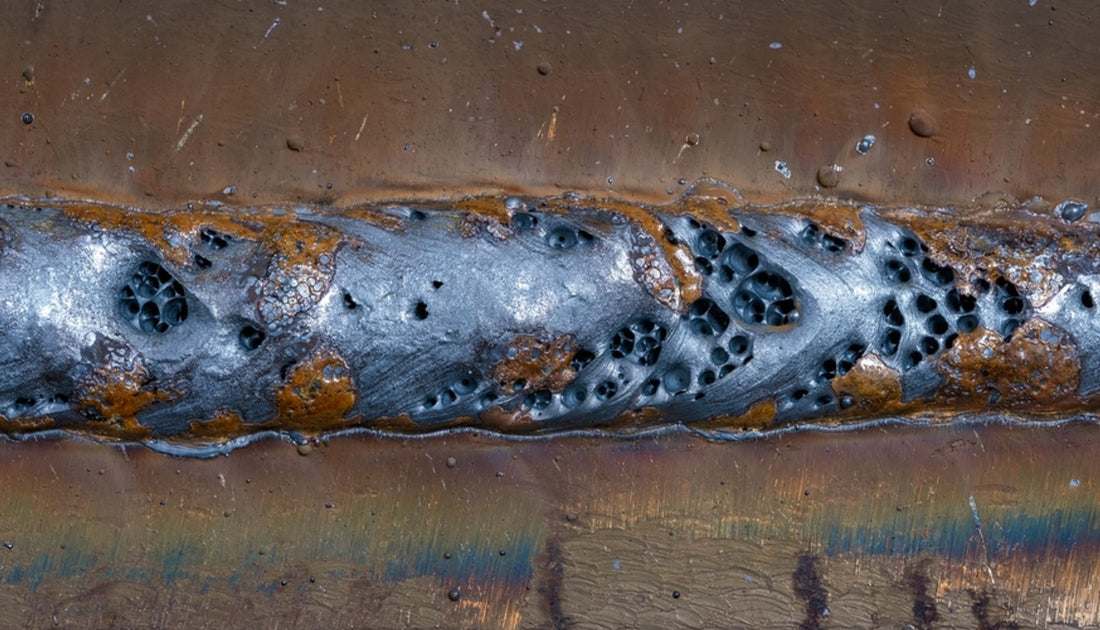
Best Practices for Quality Welds
Ensuring adherence to sector criteria and proper weld joint prep work are basic elements of achieving consistently high-quality welds. In enhancement to these fundamental steps, there are a number of best practices that welders can carry out to even more enhance the top quality of their welds. One secret practice is keeping proper sanitation in the welding location. Contaminants such as oil, oil, corrosion, and paint can detrimentally impact the quality of the weld, bring about flaws. Thoroughly cleansing the workpiece and bordering location prior to welding can help mitigate these issues.
Another best practice is to thoroughly choose the suitable welding specifications for the particular materials being signed up with. Correct criterion option makes sure ideal weld infiltration, fusion, and overall quality. Making use of premium welding consumables, such as electrodes and check that filler metals, can considerably impact the last weld high quality.
Value of Porosity Control
Porosity control plays a critical duty in making sure the stability and quality of welding joints. Porosity, characterized by the presence of cavities or gaps within the weld steel, can considerably compromise the mechanical homes and structural honesty of the weld. Extreme porosity compromises the weld, making it more susceptible to cracking, deterioration, and general failing under functional loads.
Efficient porosity control is essential for preserving the preferred mechanical properties, such as stamina, ductility, and toughness, of the bonded joint. What is Porosity. By minimizing porosity, welders can improve the total quality and dependability of the weld, ensuring that it satisfies the efficiency requirements of the desired application
Furthermore, porosity control is vital for accomplishing the desired visual appearance of the weld. Extreme porosity not just damages the weld but likewise interferes with its visual charm, which can be essential in industries where looks are necessary. Appropriate porosity control methods, such as making use of the correct protecting gas, regulating the welding criteria, and ensuring Going Here proper tidiness of the base materials, are necessary for generating high-quality welds with minimal issues.
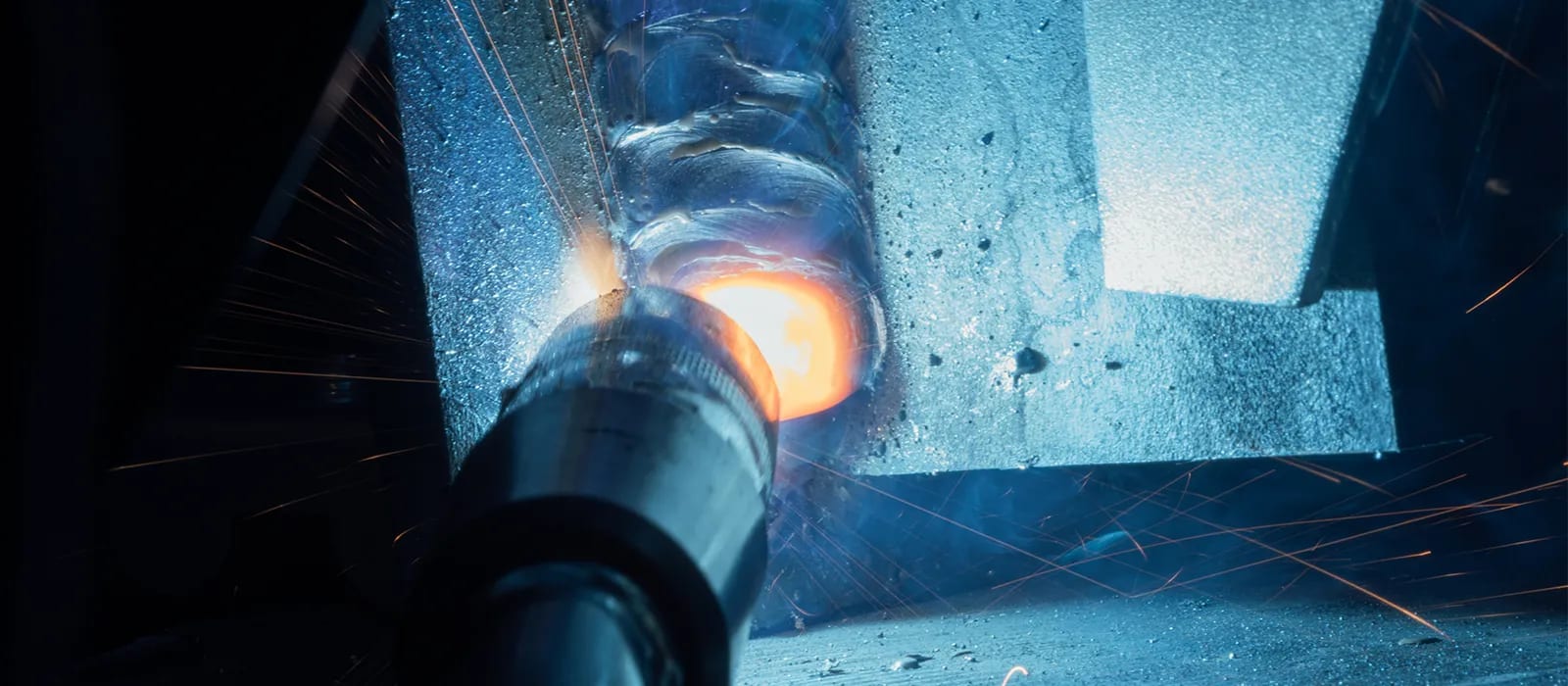
Conclusion
In conclusion, porosity in welding is a common defect that can endanger the top quality of the weld. It is crucial to regulate porosity in welding to make sure the honesty and stamina of the final product.